The Ultimate Guide to Choosing the Right Packaging Machine Repair Experts
The Ultimate Guide to Choosing the Right Packaging Machine Repair Experts
Blog Article
The Ultimate Guide to Packaging Device Repair Work: Keep Your Workflow Running Efficiently
In the world of product packaging, the performance of procedures pivots dramatically on the integrity of equipment. Recognizing the details of product packaging equipment repair is crucial for maintaining optimal efficiency and decreasing disturbances. Normal upkeep not just prolongs the life of these devices however also addresses common concerns that can hamper efficiency. As we check out the nuances of troubleshooting and the crucial decision-making process in between repair service and replacement, it comes to be clear that a proactive strategy can yield substantial benefits. What specific techniques can organizations implement to guarantee their product packaging operations remain nonstop?
Significance of Normal Maintenance
Regular maintenance of product packaging makers is essential for making certain ideal efficiency and durability. By implementing a structured upkeep routine, drivers can identify possible issues prior to they escalate into substantial problems. This positive approach not only decreases downtime but additionally extends the life expectancy of the tools, ultimately causing reduced operational prices.
Normal evaluations permit the assessment of vital parts such as belts, sensing units, and seals. Attending to damage quickly stops unanticipated failings that could interrupt manufacturing and bring about pricey repairs. Furthermore, routine upkeep assists make certain conformity with industry standards and policies, promoting a risk-free functioning setting.
In addition, upkeep tasks such as lubrication, cleaning, and calibration significantly enhance machine efficiency. Improved performance translates to consistent product quality, which is vital for maintaining consumer satisfaction and brand reputation. A well-maintained packaging equipment runs at ideal speeds and decreases material waste, adding to total performance.
Typical Packaging Device Issues
Product packaging equipments, like any type of complicated machinery, can encounter a selection of typical problems that may prevent their efficiency and effectiveness - packaging machine repair. One prevalent trouble is irregular sealing, which can lead to item putridity and wastage if plans are not appropriately sealed. This often arises from misaligned elements or worn securing components
An additional constant problem is mechanical jams, which can happen due to foreign items, used parts, or inappropriate positioning. Jams can cause hold-ups in production and rise downtime, eventually affecting total efficiency. In addition, electronic breakdowns, such as failure in sensing units or control systems, can interrupt procedures and lead to unreliable dimensions or unpredictable machine habits.
Furthermore, problems with item feed can likewise arise, where products might not be provided to the product packaging area constantly, causing disruptions. Wear and tear on belts and rollers can lead to suboptimal performance, needing prompt attention to stop more damage.
Comprehending these typical concerns is vital for preserving the stability of product packaging procedures, guaranteeing that machinery runs efficiently and successfully, which in turn helps in meeting production targets and keeping item top quality.
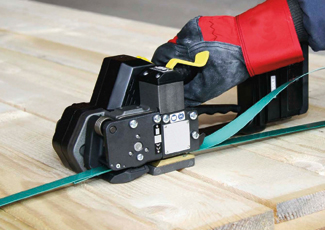
Repairing Methods
Effective repairing methods are essential for without delay attending to issues that emerge with packaging equipments. A methodical approach is crucial for identifying the origin cause of breakdowns and minimizing downtime. Begin by collecting information concerning the symptoms observed; this might include unusual sounds, operational hold-ups, or mistake codes shown on the equipment's interface.
Following, refer to the device's guidebook for troubleshooting standards specific to the design in inquiry. This resource can supply valuable insights right into usual issues and suggested analysis steps. Use aesthetic inspections to inspect for loosened links, worn belts, or misaligned elements, as these physical aspects often contribute to functional failings.
Implement a process of elimination by screening specific machine functions. For example, if a seal is not creating appropriately, assess the sealing system and temperature level settings to identify if they meet operational specs. Paper each action taken and the outcomes observed, as this can assist in future repairing initiatives.
Fixing vs. Substitute Choices
When confronted with equipment breakdowns, determining whether to replace a product packaging or repair maker can be a facility and crucial selection. This choice rests on a number of essential variables, consisting of the age of the equipment, the degree of the damage, and the forecasted influence on operational performance.
First of all, think about the machine's age. Older equipments might need more constant repair work, leading to greater advancing costs that can go beyond the investment in a new device. Furthermore, review the intensity of the malfunction. Small problems can often be settled swiftly and affordably, whereas considerable click to find out more damage could require a significant monetary commitment for repair services.
Operational downtime is one more crucial consideration. Investing in a new maker that supplies enhanced effectiveness and integrity could be more prudent if fixing the equipment will certainly cause extended hold-ups. Think about the accessibility of parts; if substitute elements are difficult to come by, it might be extra critical to change the equipment entirely.
Ultimately, performing a cost-benefit analysis that includes both long-term and immediate implications will certainly assist in making an educated choice that straightens with your functional objectives and monetary restrictions. (packaging machine repair)
Preventive Actions for Long Life

Trick preventive steps include routine lubrication of relocating components, placement checks, and calibration of sensing units and controls. Developing a cleansing schedule to remove debris and contaminants from machinery can considerably minimize deterioration (packaging machine repair). In addition, checking functional criteria such as temperature level and resonance can aid identify abnormalities beforehand
Educating team to identify indications of wear or breakdown is one more important element of precautionary maintenance. Empowering operators with the expertise to execute basic troubleshooting can cause quicker resolutions straight from the source and reduce operational disruptions.
Documents of upkeep tasks, consisting of solution documents and examination searchings for, promotes responsibility and helps with informed decision-making regarding fixings and substitutes. By focusing on safety nets, companies can guarantee their product packaging makers operate at peak efficiency, eventually resulting in increased performance and decreased operational prices.
Final Thought
In verdict, the effective maintenance and repair service of product packaging machines are critical for maintaining functional performance. By implementing precautionary procedures, organizations can boost machine longevity and wikipedia reference guarantee undisturbed performance in product packaging procedures.
Understanding the intricacies of packaging device repair work is vital for keeping optimum efficiency and decreasing disturbances.Normal upkeep of product packaging equipments is critical for making certain optimum efficiency and long life.Product packaging makers, like any type of complicated machinery, can experience a range of common issues that may prevent their efficiency and performance. If repairing the device will cause long term hold-ups, spending in a new machine that offers boosted performance and dependability might be more sensible.In verdict, the efficient maintenance and repair of product packaging makers are critical for sustaining functional effectiveness.
Report this page